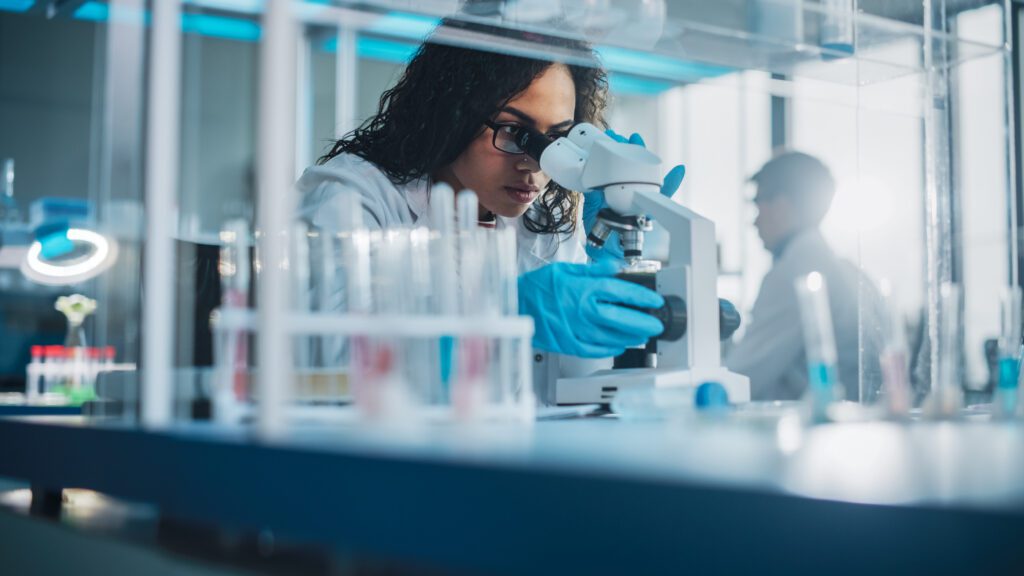
Hemocompatible coatings are needed not only to minimize the risk of thrombus formation but also to prevent bacterial adhesion as well as to inhibit inflammatory response and promote endothelization. This means that the coating is biocompatible & encourages the growth of endothelial cells on the device surface.
These cells are what make up the inner lining of all blood vessels and, as one would expect, are extremely hemocompatible. The growth of these cells on the surface of a medical device, especially in the case of stents and flow diverters, would make it significantly more hemocompatible and would enhance the overall lifetime of the device. It is for this reason that a coating that is both hemocompatible as well as promotes endothelialization would be seen as the gold standard in the field, both of which can be achieved with Smart Reactors’ proprietary coating technology CamouflageTM.
Properties of a Hemocompatible Coatings
There are a variety of factors that influence the hemocompatibility of a coating. The first of which is the wettability of the coating. This relates to how a coating interacts with a fluid which in this case is blood. A coating should increase the wettability of a device or in other words make the device surface hydrophilic. This will lower the surface interactions between the device and the blood components decreasing the risk of activating the mechanism of blood coagulation.
This is compared to a surface that has a lower wettability or is hydrophobic in nature. In this case, the device surface would have higher surface interactions with the blood and therefore adsorb more blood proteins. This alters the function of the proteins promoting cell adhesion and initiating thrombus formation.
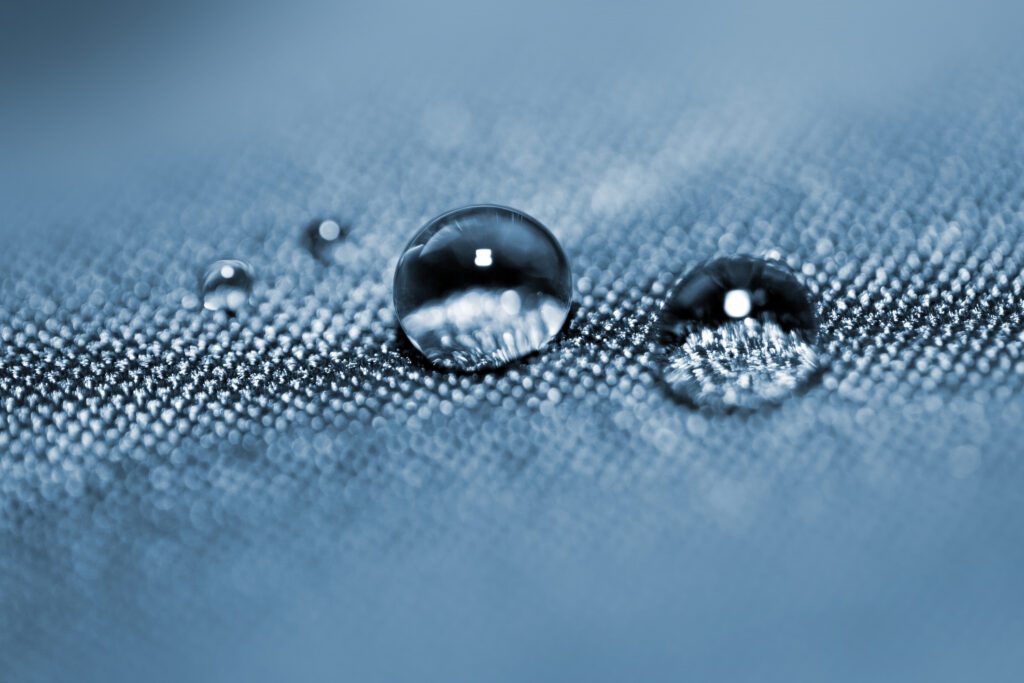
It is also vital that the materials used within a hemocompatible coating are non-toxic and the coating itself has a high level of durability. In conjunction with making a device more hemocompatible, a coating cannot cause damage or be toxic to existing cells within the blood or the vessels. It should in fact, as previously discussed, allow cell growth on the surface of the coated device to promote long-term hemocompatibility.
The durability performance requirements of the coating is also something that needs to be considered when discussing device longevity. This is because if the coating were to have a low level of durability and came off of the device prior to its intended use, this would then expose its non-hemocompatible surfaces which would increase the risk of clotting cascade and lead to potential device failure and replacement. Any potential risks of thrombus formation further down the line would be detrimental to a patient’s health.
Finally, it is important that a coating can be applied uniformly while also only forming a thin layer typically at sub-micron level. This is to ensure that the coating doesn’t inhibit the intended function of the device, in particular Gas Exchange functionality in an ECMO or CPB system design. Adequate uniformity of the coating ensures that the applied material is evenly distributed and that the device is fully covered to prevent any exposure areas of the original material that the medical device is made of to minimize the risk of adverse reactions.
Different Types of Hemocompatible Coatings
There are many different types of hemocompatible coatings on the market, all of which fall into two main categories, active or passive coatings. An active coating is one that contains a pharmaceutical anticoagulant that can be secreted into the blood or immobilized onto the device service to inhibit blood clot formation. This is compared to a passive coating which minimizes the interactions with the blood defense systems without the use of pharmaceuticals.
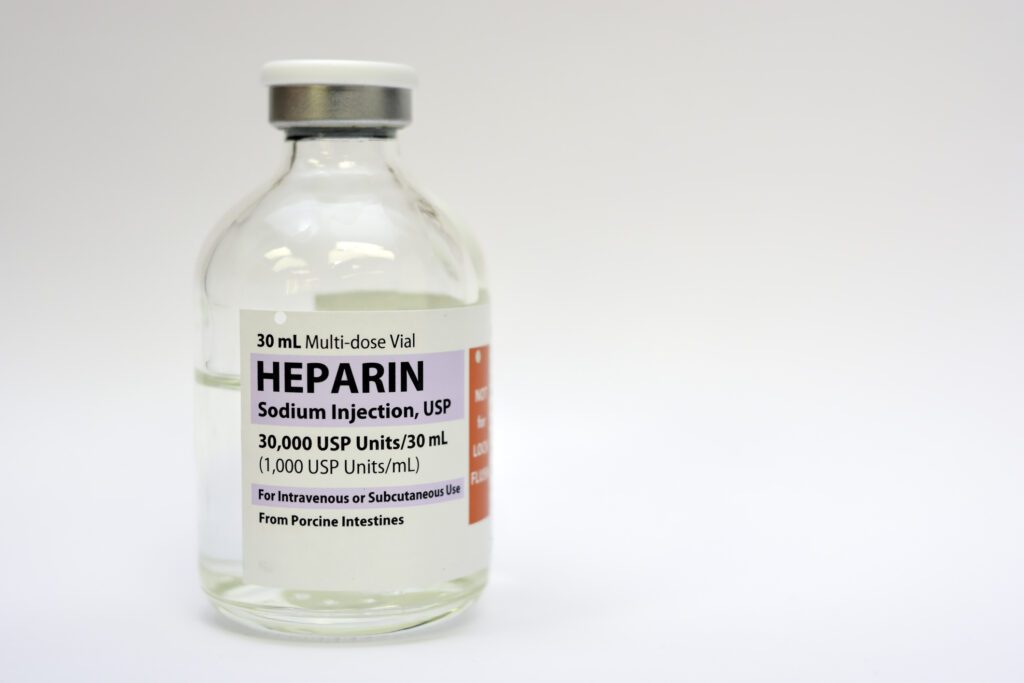
One of the main examples of an active coating and a major component used in a lot of today’s hemocompatible coatings is heparin. This is a commonly used, albeit expensive, anticoagulant and can be either immobilized on a device’s surface through enhanced surface functionalization or it can be secreted into the bloodstream at the site of the implanted device. Heparin works as a hemocompatible coating by accelerating the inhibitory activity of antithrombin, which is a substance in the blood that limits blood clotting as well as being the primary inhibitor of thrombin which is a main constituent within the coagulation pathway. Heparin has also been shown to be combined with other materials, such as polymers or proteins, to create a more well-rounded coating. While heparin is widely used within the field of hemocompatible coatings there are many challenges that go along with it. For example, as these coatings are made using pharmaceuticals, they are much harder to bring to market having more stringent regulatory pathways.
The latest MDR changes, particularly Rule -14 will pose significant challenges for Heparin-based hemocompatible surface coatings. Heparin surface coatings are significantly more expensive than their non-medicinal and are well known to have unfavorable side effects within the body such as heparin-induced thrombocytopenia (HIT) caused by an allergic reaction to heparin. If this occurs the patient may react in a way that may cause blood clots rather than preventing them.
Phosphorylcholine (PC) is one of the most widely used examples of a passive hemocompatible coating. PC is the chemical name of the polar head group found in many phospholipids particularly those that form the bilayers that make up a cell membrane. This material plays a key role in deciding how a cell interacts with its surrounding environment and it is responsible for the biocompatibility that exists between most cells. PC has a natural affinity to water, which means that coatings that contain the PC group are essentially surrounded by a molecular layer of water. This effectively makes the device surface biologically inert, reducing the risk of blood clot formation as it disguises the surface such that the proteins within the blood do not respond to the foreign body.
Like heparin, there are a variety of disadvantages associated with using a PC-based hemocompatible coating. Firstly, for the fabrication of these layers, the use of harsh chemical solvents is needed, this can make integrating the coating procedure into device manufacturing more difficult. Secondly, PC coatings are not designed to promote endothelialization, which majorly influences the long-term hemocompatibility of these coatings. This would be considered one of the major drawbacks of PC-based coatings as it does limit its applications.
Smart Reactors– Camouflage™
Another example of a non-medicinal passive coating is CamouflageTM coating technology, developed and commercially licensed by Smart Reactors Ltd, Ireland. This coating is quickly becoming the 1st choice coating for many blood-contacting devices due to its versatility and high performance.
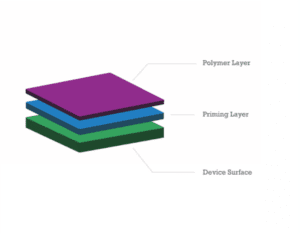
This coating is made up of a synthetic polymer and a protein base layer. The use of the protein base layer is multi-functional as it firstly allows for the coating to stick to virtually any substrate without the use of any surface preparation or functionalization. This is highly advantageous when adding the coating step into any device manufacturing process.
Also, the use of non-inflammatory proteins allows the coated device to be masked by the circulatory blood and reduces the body’s reaction to the foreign surface. This coating technology is non-toxic as well as shows exceptional hydrophilic properties which as previously mentioned are requirements for a good hemocompatible coating.
It is also highly durable while also maintaining an invisible thickness at the nanoscale level. The coating is water-based, meaning that it does not require the use of harsh chemical solvents in the fabrication process, unlike PC coatings.
Due to its passive nature and non-medicinal properties, it offers a significantly faster regulatory pathway than that of heparin surface coatings.
Furthermore, CamouflageTM promotes endothelialization on the surface of the coated medical device, while increasing its hemocompatible properties and device longevity.
What to Consider when Picking a Hemocompatible Coating
There are many factors that come into consideration when determining the best hemocompatible coating for your device. The illustrations below show a variety of medical devices that require hemocompatible coatings as well as the important properties that the hemocompatible coating must have to be deemed effective. These include stents, flow diverters, perfusion equipment, and extracorporeal membrane oxygenators (ECMO).
For all devices, it is clear that any applied coating must improve hemocompatibility while having a high level of durability and uniformity. In the case of stents and flow diverters, it is also extremely important for the coating to promote endothelialization. Finally, in the case of ECMO, it is highly important that the level of gas exchange is not inhibited by the applied hemocompatible coating as this would have an effect on device performance.
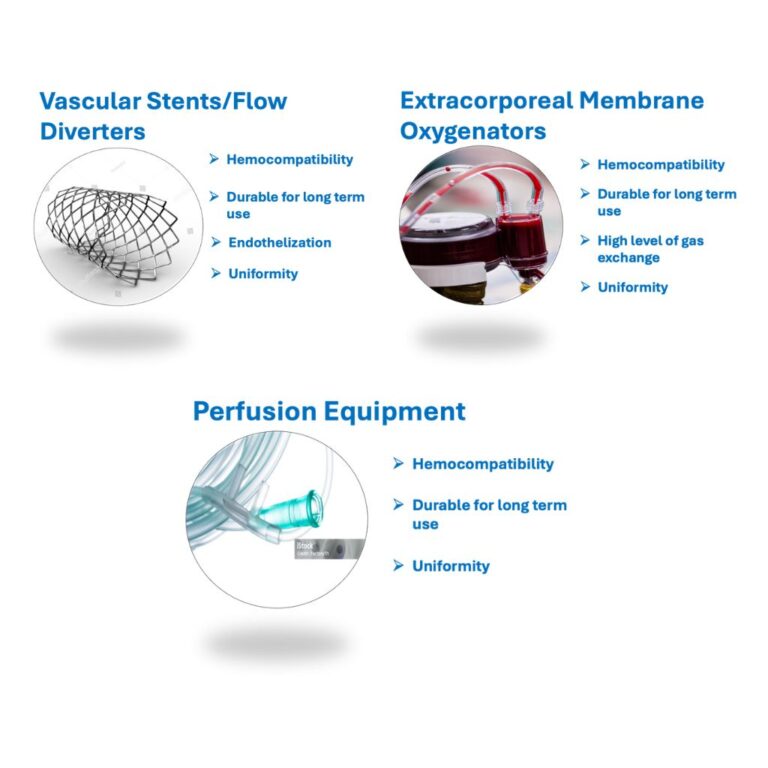
All of the required properties for each of the devices seen above can be achieved using Smart Reactors Camouflage™ hemocompatible coating. This coating technology is quickly being adopted by Medical device manufacturers on a global basis. Camouflage™ has been proven to have a high level of hemocompatibility through in-depth in-vitro analysis while also promoting endothelization.
Other studies have shown that the Camouflage™ coating does not impede Gas Exchange & facilitates high levels of gas exchange in ECMO devices making it an extremely versatile coating for many medical Devices.
The answer to all your Hemocompatible & Endothelialization needs is Camouflage™
Share this post: on LinkedIn